The control management system of water treatment plant is a distributed computer control system (namely the distributed control system) based on the modern advanced control thoughts, it has integrated the characteristics of modern computer technology, high-performance controller as well as the intelligent instruments; therefore it has played a huge role in terms of the operation and management of water treatment plant.
The detecting control system--local control station is composed of the programmable logic controllers (PLC) and the automatic instruments to control the subareas as the objects; it has the independent ability for area control and could be regulated and controlled by the central control, however it doesn’t rely on the existence of the central control but carry out decentralized control to all processes of the water treatment plant; and then the central control room shall carry out the centralized management to the entire plant. The local control stations are set inside the buildings with relatively centralized control objects and signal sources according to the panel layout of the technologies and structures adopted by the water treatment plant.
System Functions
?Management and control integration----by the advanced means of computer and network, it has realized the management and control integration of diversion and purification or decontamination and water supply and drainage systems of the water treatment plant, so as to form the comprehensive information management system containing the production scheduling, matter information management and supervisory control.
?Realization of dynamic production scheduling---reflect the data collected automatically as well as the real-time data of production scheduling through the network, after analyzing the data, the processed information such as water quality and energy consumption will be represented in forms of chart or figure so that the leaders and management personnel could make judgments in line with the realities and give commands to instruct the production according to their experience and knowledge in time.
?Possibility of realizing the advanced process control and optimization of the production process---on base of using the complete data source and computing ability of the computer, the mathematical model of advanced control can be developed to improve the output and quality directly relating to the economic benefits and reduce the raw materials and energy consumption so as to obtain the considerable economic and social benefits. As a result, the operation of water treatment plant will develop towards the systemic, information-based and scientific production mode and achieve the goal of improving the economic benefits and market competitiveness eventually.
Technical Scheme of the Water-treatment Plant Automation Monitoring System
1. System Profile
With the continuous development and improvement of scientific and technical levels, the computer system-based management for production goes increasingly deeper into the enterprises of all professions and trades. Therefore it is not only practicable but also capable of comprehensively improving the management levels and production efficiencies of the enterprises so as to increase the production profits by establishing an automation control system on the core of computer to carry out the comprehensive management to the sewage plant.
This sewage plant engineering monitoring system contains the monitoring and control to the entire sewage processing in the plant. Within the entire production area, it contains the coarse interjoist, sewage lift pump room, fine interjoist, Jones grit chamber, biochemical pool, sedimentation tank, backflow and excess sludge pump room, sludge-storage pool, sludge concentration and dewatering room, water-exit flowmeter well, ultraviolet disinfection canal as well as the general power transformation and distribution room, etc. these processes can be comprehensively monitored and controlled through this monitoring system; meanwhile, through this monitoring system, these controls can not only carries out through the monitoring center but also adopting the method of closed-ring .
As for the sewage plant computer monitoring system, it is suitable to adopt a computer monitoring system of the secondary management, its upper system is in the central control room and used to monitor all stations and equipments inside the plant; while the lower systems are at all PLC stations and realized through PLC; the upper and lower systems exchange data through the communication network; both the upper and lower systems could monitor and control the equipments inside the system through the network; however the lower systems could only monitor the local stations and equipments, while the upper system could monitor all stations and equipments.
In terms of the system functions, the sewage plant computer monitoring system is composed of three layers: the management computer subsystem, the monitoring computer subsystem and the local control stations. The management computer subsystem and monitoring computer subsystem belong to the upper system and are connected through the Ethernet; the monitoring computer subsystem and local control stations exchange data through the industrial Ethernet while the local control stations belong to the lower system.
The monitoring system of this sewage plant engineering is composed of the upper-terminal system and instrument detecting system made up by PLC and the computer monitoring management system, in which the management computer subsystem in the upper-terminal system is composed of the data server, production management and office computer as well as the network switch and printer; while the monitoring computer subsystem is composed of 2 central monitoring computers, projector system, printer and the industrial network switch.
Overall Structure of the Monitoring System
Set the central control room (CCR) inside the comprehensive office area of the sewage plant to centrally monitor, control and manage the entire production process and technology process of the sewage plant so as to realize the on-line real-time monitoring to the automatic control, alarm, protection, operation and regulation during the production process as well as the important parameters during all technology processes and carry out the real-time monitoring to the working conditions of the process and equipment inside the plant.
The management computer subsystem of the central control room adopts the computer network with the B/S (Browser/Server) structural style so as to compose the 100M switch-based local area network on the core of a data network server; the monitoring computer subsystem adopts the C/S(Customer/Server) structure and the monitoring working station adopts the redundant configurations so as to improve the data safety.
The monitoring computer subsystem of the central control room and all single PLC control systems inside the plant are connected by the optical fiber rig, and the network form is industrial Ethernet with the transmission rate of 100M.
Set a data server, network printer and office computer inside the central control room to form the management computer subsystem. It provides the entire in-plant information management structure for the production, operation, management, decision-making, production scheduling, building digital information transmission platform for daily office as well as connecting the monitoring computer subsystem and office management terminal of the entire plant. The management network construction completes the works such as basic hardware platform, basic software, database of the production process automation control subsystem as well as access of the production process automation control subsystem through WEB. According to the application requirements, the management computer subsystem contains the subsystem for assistant decision-making of production and operation, subsystem for management command of production scheduling, subsystem for device management and subsystem for the comprehensive office management.
Set 2 monitoring working stations inside the central control room, both machines hot standby. Under the normal circumstances, one is used for the process monitoring and the other is ready to replace the fault device as the backup. The 2 operating stations have the same hardware and software configurations, while the functions and monitored objects can be interchanged. What’s more, there are 2 printers and projectors so that they could form a complete monitoring computer subsystem.
At the same time, during the soft and hard designs of the central control system according to the system planning as well as the demands in the future, the interfaces for 1~2 single control systems need to be added in the long-term forward engineering will be reserved. The Ethernet network interface will be reserved in the central system so as to connect with the office automation system to realize the data sharing as well as integration of production and management inside the engineering.
Overall Configuration of the Computer Monitoring System
Overall Structure of the Automatic System
The overall structure of automatic system is as shown in the following figure:
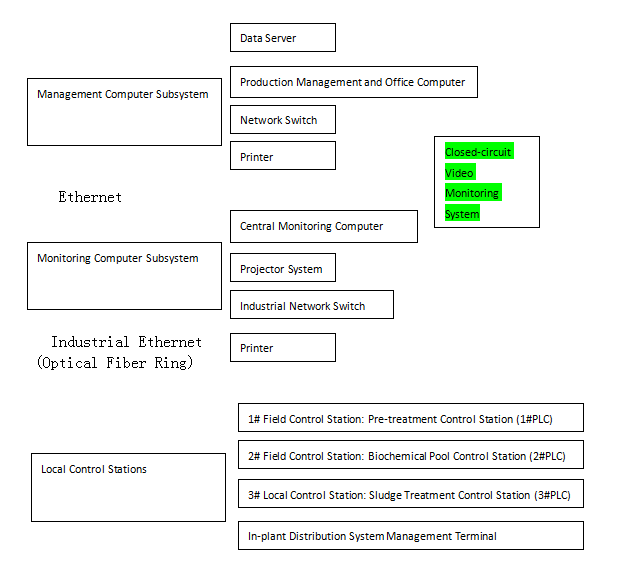
The entire system is composed of three layers: the management computer subsystem, monitoring computer subsystem and local control stations.
The management computer subsystem is composed of data server, production management and office computer, network switch and printer.
The management computer subsystem and monitoring computer subsystem are connected through the Ethernet.
Monitoring Computer Subsystem
The monitoring computer subsystem is composed of two central monitoring computers, projector system, printer and industrial network switch.
The monitoring computer subsystem and local control stations exchange data through the industrial Ethernet ring.
Local Control Stations
According to the process characteristics as well as the structure plane layout, there are three local control stations and one power transformation and distribution system management terminal are established. The central monitoring computer, local PLC control stations and power distribution system management terminal compose the industrial Ethernet optical fiber ring through the industrial network switch. The local PLC control stations are connected to the local instruments through the shielded cables.
In addition, the system contains a closed-circuit video monitoring system as an independent system. The monitoring center is also configured inside the central control room (See the chapter of the closed-circuit video monitoring system for details).
Management Computer Subsystem Configuration
The management computer subsystem provides the entire in-plant information management structure for the production, operation, management, decision-making, production scheduling, building digital information transmission platform for daily office as well as connecting the monitoring computer subsystem and office management terminal of the entire plant. The management network construction completes the works such as basic hardware platform, basic software, database of the production process automation control subsystem as well as access of the production process automation control subsystem through WEB.
Management Computer Subsystem Composition
As shown in the following figure:
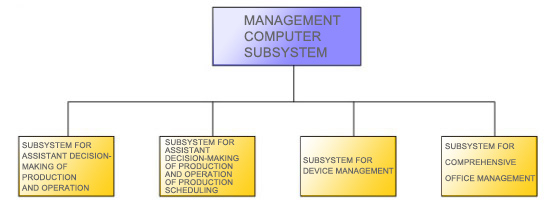
According to the functions of the management systems, they can be divided into: subsystem for assistant decision-making of production and operation, subsystem for management command of production scheduling, subsystem for device management and subsystem for the comprehensive office management.
Subsystem for Assistant Decision of Production and Operation
It could provide the necessary synthesized production and operation information to the decision-making levels so as to make necessary analysis and processing and provide the assistant support for decision-making.
Subsystem for Management Command of Production Scheduling
It has various kinds of measures for data monitoring which could display the real-time data in the form of not only table but also figure, including various forms such as alarm tone etc. And it could also send out the special instructions.
Subsystem for Device Management
On the core of use, maintenance and repair of the device, it effectively records, reflects, counts and analyzes the device technical data and daily device management activities under categories.
Subsystem for the Comprehensive Office Management
Starting from the global, flexible and standard design ideas, this system adopts the advanced processing technology for document database to provide the integrated working environment for office staff, leaders and cadres at all levels. This system has rich and practicable functions, friendly operation interface as well as the flexible extendibility; therefore it is convenient to process various kinds of data, graphic, voice and image information, what’s more, it is safe and reliable. It mainly contains functions of the general MIS (Management Information System) and it is the important component of the office automation; it involves all aspects of human, wealth, materials and etc.
Configuration and Structure of the Management Computer Subsystem
The equipment configuration and structure are as shown in the following figure:
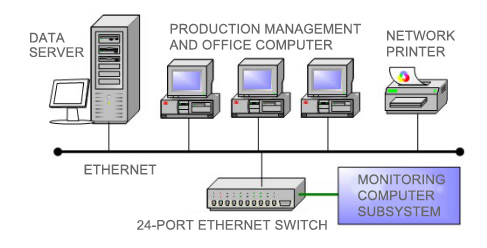
Configuration of Monitoring Computer Subsystem and Local Control Stations
Configuration structure of the monitoring computer subsystem and local control stations
The equipment configuration and structure are as shown in the following figure:
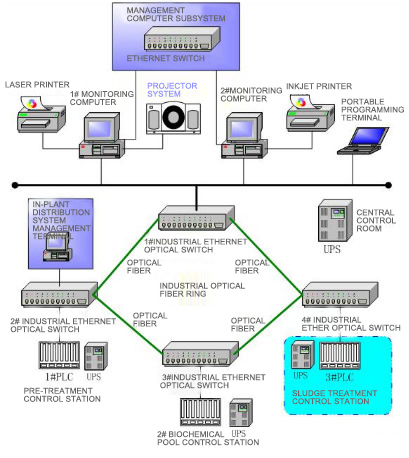
Power transformation and distribution system management terminal contains: in-plant power transformation and distribution system management terminal, this system 1#PLC or the central monitoring computer collects various kinds of real-time information about the in-plant power transformation and distribution system through this management terminal.
The local control stations contain: the pre-treatment control station (1#PLC), biochemical pool control station (2#PLC) and sludge treatment control station (3#PLC). In which the pre-treatment control station (1#PLC) and the in-plant power transformation and distribution system management terminal carry out the data communication through the 2# industrial switch. The biochemical pool control station (2#PLC) is connected to the optical fiber industrial Ethernet ring through the 3# industrial network switch. The sludge treatment control station (3# PLC, this PLC is supplied by other manufacturers and establishes an independent control system) is connected to the optical fiber industrial Ethernet ring through the 4# industrial network switch. The central monitoring computer is connected to the optical fiber industrial Ethernet ring through the 1# industrial switch so as to exchange data with the local control stations.
Control Methods of the System
Control Methods:
The local manual mode: when the “On-the-spot/Remote” switch on the local control box or MCC control cabinet of the equipment selects the “On-the-spot” method, the start/stop, on/off operation for the equipment can be realized through the buttons on the local control box or MCC control cabinet;
On-the-spot overhaul mode: when the “On-the-spot/Remote” switch on the local control box or MCC control cabinet selects the “Remote” mode, the equipment control power is in the LCS (Local control station). The operators can select the “Manual” method through the operation panel of the LCS control station, and use the monitoring screens or keyboards to carry out the overhaul operation to the equipment;
Remote mode: namely the remote manual control method. When the “On-the-spot/Remote” switch on the local control box or MCC control cabinet selects the “Remote” method, the operators can use the mouse or keyboards to select the “Remote” method to carry out the start/stop, on/off operation for the equipment through the monitoring screens of the operation panel or the central control system operation station;
Automatic mode: when the “On-the-spot/Remote” switch on the local control box or MCC control cabinet selects the “Remote” method, and the “Automatic/Remote” of the local control station is set as the “Automatic” method, the operation of the equipment is completely controlled by the PLC/RTU by completing the operation or on/off control of the equipment according to the working conditions as well as the production requirements of the sewage plant without the manual intervention.
Priority Levels of the Control Methods
The local manual control method is of the highest priority level of among the entire control system, and the remote control and auto-control are set on this basis.
The control levels are arranged from high to low as: local manual control, on-the-spot overhaul control, remote control and auto-control;
The manual intervention is exclusive to the operators, for the process chain is invalid under this mode; while under the automatic mode, the safety chain is valid and limits the possibility of operation so as to prevent the operation under the abnormal condition. The closer the control layer is to the technology process, the higher priority it gets.
Communication Network Structure of the Monitoring System
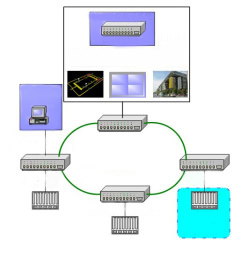